In the world of process documentation, two key elements often get muddled: Standard Operating Procedures (SOPs) and Work Instructions. Both are crucial for the seamless operation of any business, but they serve distinctly different purposes. Understanding the nuances between them is not just a matter of terminology but a way to ensure efficiency and quality in the execution of tasks.
The Essence of Standard Operating Procedures
At its core, a Standard Operating Procedure is a high-level document that outlines a set of instructions to execute a routine operation. SOPs are often used in various industries to ensure consistency and quality of service or product. These documents are comprehensive and provide an overview of tasks, often encapsulating multiple steps of a process.
Imagine an SOP as a roadmap. It gives you the direction and the major landmarks, but it doesn’t detail every turn and street. For instance, an SOP for a pharmaceutical company might detail the procedure for quality control testing. It would cover the scope of the testing, the objectives, and the key responsibilities, but it wouldn’t specify the nitty-gritty of conducting each test. Learn more about standard operating procedures over at Lean Community.
The Specificity of Work Instructions
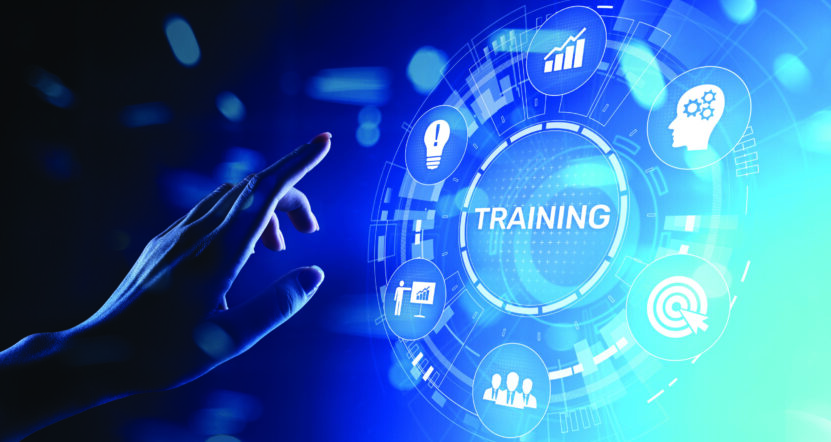
Work Instructions take a narrower focus compared to SOPs. They are the step-by-step guides to performing a single task within the larger process outlined by an SOP. If an SOP is the roadmap, Work Instructions are the turn-by-turn directions. They are much more detailed and specific, often including exact measurements, times, and detailed actions.
In our previous example, a Work Instruction under the SOP for quality control might detail the specific steps to calibrate a piece of equipment used in testing. It would list each action required, from turning on the machine to adjusting settings, ensuring that anyone following these instructions would perform the task identically.
Different Audiences and Purposes
The audience for SOPs and Work Instructions is slightly different due to the nature of their content. SOPs are typically designed for a broader audience, sometimes even extending to external stakeholders. They provide a comprehensive overview that is useful for training, compliance, and overviewing processes.
In contrast, Work Instructions are often written for the personnel who will be directly performing the tasks. They are practical, detailed, and focused, serving as a direct guide for employees in their day-to-day work.
The Role in Compliance and Quality Control
Both SOPs and Work Instructions play a significant role in compliance and quality control, but in slightly different ways. SOPs are often used as a reference in audits and compliance checks. They demonstrate that a company has a structured process in place and is aware of industry standards and regulations.
Work Instructions, on the other hand, are crucial for maintaining day-to-day quality control. They ensure that each task is performed consistently and accurately, reducing the risk of errors and maintaining the quality of the output.
Flexibility and Rigidity in Documentation
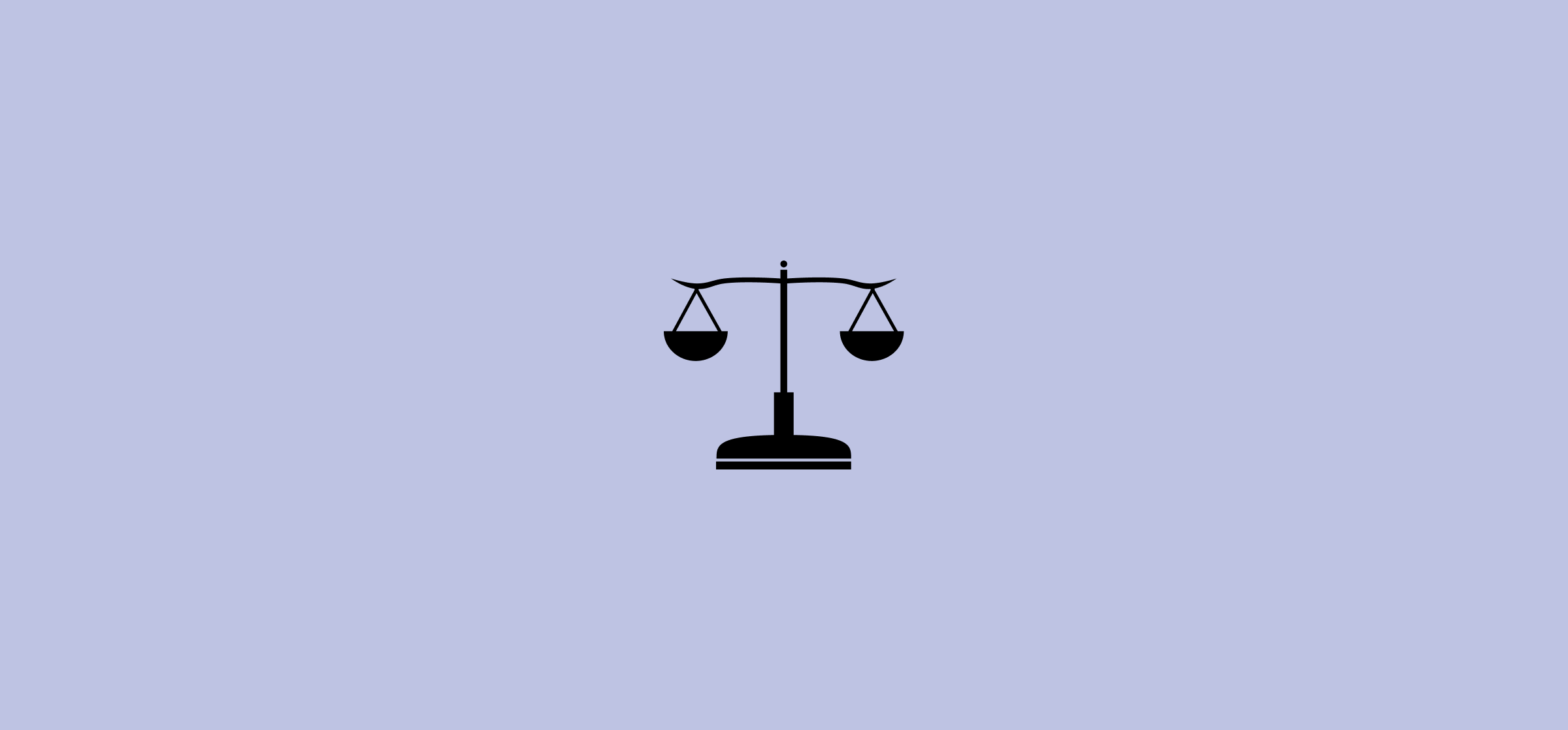
Another key difference lies in the flexibility of these documents. SOPs, while detailed, offer a degree of flexibility. They outline the what and the why but often leave the how to be determined by the specific circumstances or the professional discretion of the staff.
Work Instructions are far less flexible. They need to be strictly followed to ensure uniformity, especially in industries where precision is critical, such as manufacturing or pharmaceuticals. Deviating from Work Instructions can lead to inconsistencies in the product or service quality.
Integration and Coherence
The most effective process documentation systems integrate SOPs and Work Instructions coherently. An SOP should seamlessly lead into its corresponding Work Instructions, and employees should understand how the two relate. This integration ensures that the overarching process is efficient and that each task within it is performed accurately.
Evolving with Organizational Needs
As organizations grow and evolve, so do their processes and the need for clear documentation. The dynamic nature of business means that both SOPs and Work Instructions must be regularly reviewed and updated. This is not just to keep up with the changes in procedures but also to incorporate feedback from those who use these documents daily.
The process of updating SOPs often involves a broader review, looking at changes in regulations, industry standards, or the strategic direction of the business. For Work Instructions, updates may be more frequent, reflecting changes in equipment, materials, or techniques.
Ensuring Accessibility and Clarity
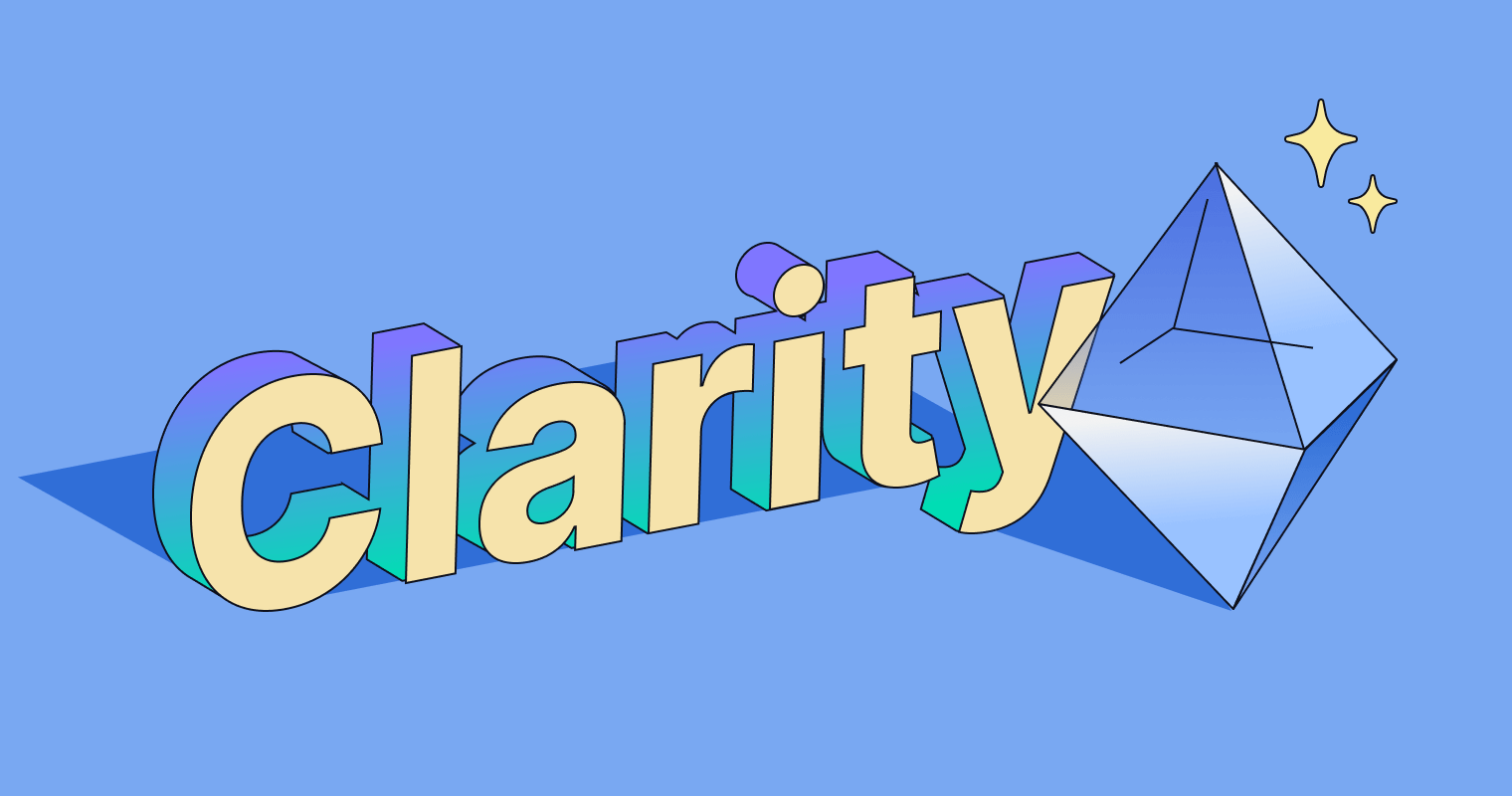
A crucial aspect of both SOPs and Work Instructions is their accessibility and clarity. These documents should be easily understandable to their intended audience. Clarity ensures that procedures are followed accurately and consistently, which is crucial for maintaining quality and efficiency.
This means avoiding jargon or technical terms that might be unclear to some readers, using clear and concise language, and structuring the document in a way that is easy to follow. In many cases, including diagrams, flowcharts, or pictures in Work Instructions can be particularly helpful.
Training and Employee Engagement
An often-overlooked aspect of process documentation is its role in training and employee engagement. Well-written SOPs and Work Instructions not only serve as training materials for new employees but also as a reference for existing staff.
Engaging employees in the creation and review of these documents can also be beneficial, as it ensures the content is practical and grounded in the reality of their day-to-day work.
Continuous Improvement and Feedback Loops
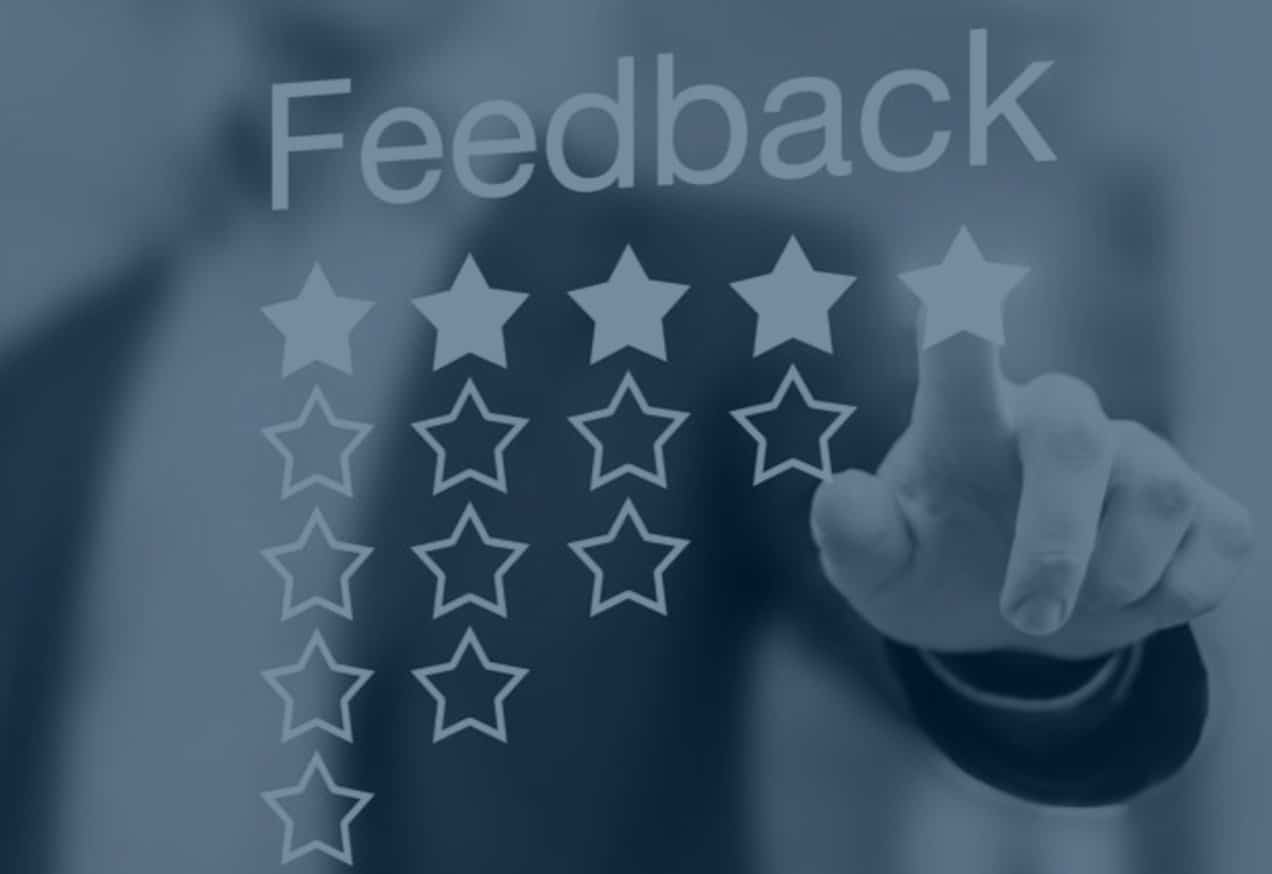
Implementing a system for continuous improvement and feedback is essential for maintaining effective SOPs and Work Instructions. This involves regularly soliciting feedback from employees who use these documents and incorporating their insights into revisions.
Continuous improvement in process documentation is not just about correcting errors or omissions. It’s about adapting to changes in the workplace, embracing new technologies, and finding more efficient ways to perform tasks. This approach ensures that SOPs and Work Instructions remain relevant and useful over time.
End Note
In essence, SOPs and Work Instructions are more than just documents – they are integral tools that guide the operations of an organization. While they serve different purposes, their effectiveness lies in how well they are integrated and aligned with each other. A well-structured SOP provides the framework within which detailed Work Instructions operate, ensuring that every aspect of a process is carried out efficiently and effectively.